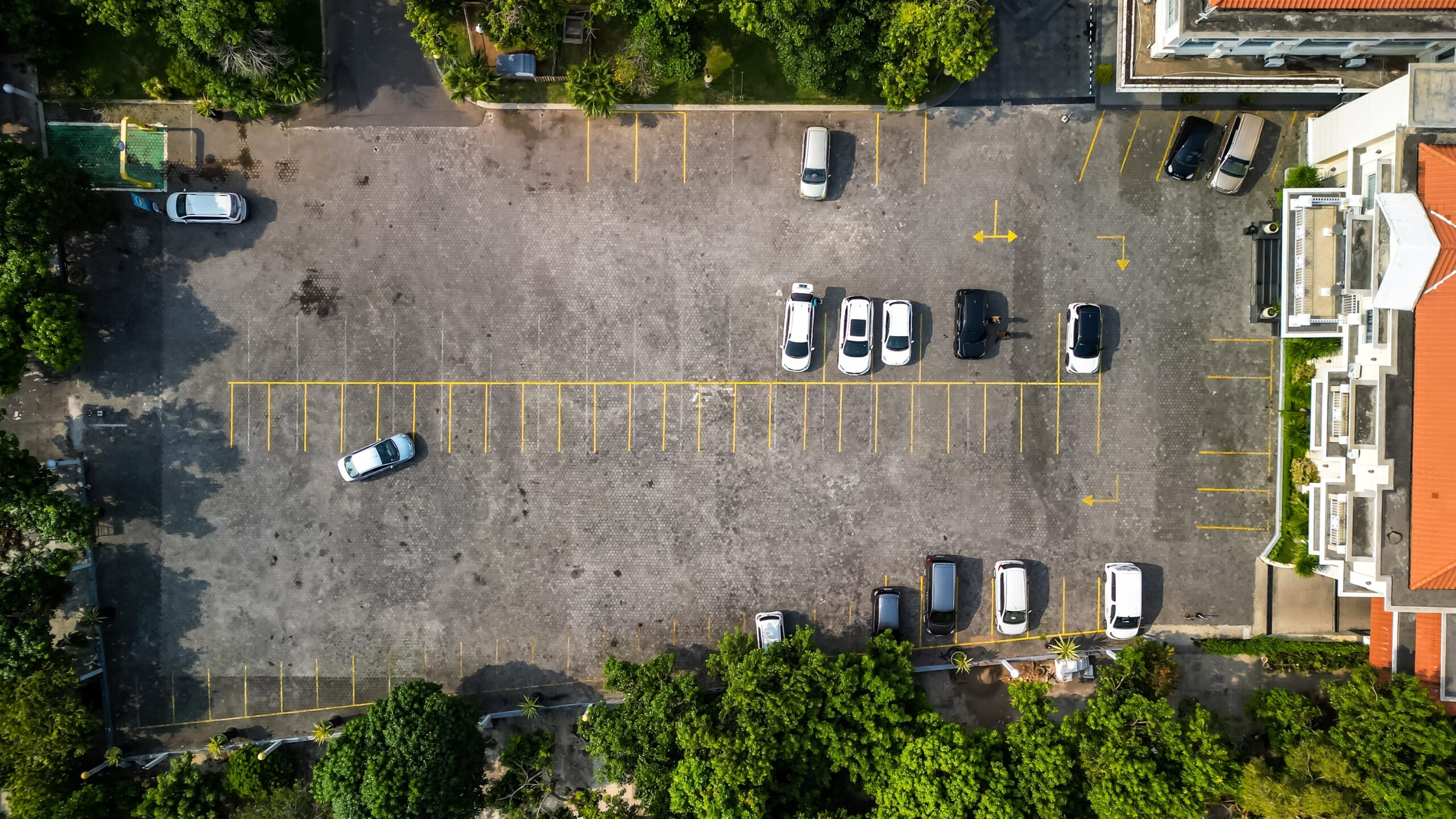
A damaged, faded, or uneven parking lot can feel like no big deal until it starts costing you money, customers, and credibility. First impressions count, and often, your parking lot is the very first interaction a customer has with your business.
Whether it’s a pothole that eats tires, faded striping that causes confusion, or water pooling into lakes after it rains, these issues all signal one thing: neglect. And neglect doesn’t just scare off customers; it leads to lawsuits, expensive repairs, and a slow erosion of trust.
But the good part? You can fix all of it. In this complete guide, we’ll break down the most common parking lot problems, how they cost you more than you think, and how to solve them smartly with long-term value in mind.
What People Face in Their Parking Lots (And Why These Problems Are More Serious Than They Look)
Your parking lot is more than just a place to park cars; it’s a reflection of your business, a safety zone for foot and vehicle traffic, and a long-term investment in your property. Yet, for many commercial property owners, serious issues creep in slowly, often overlooked until they turn into expensive liabilities. Cracks, uneven patches, poor drainage, or faded lines might look harmless at first, but every one of these issues leads to functional, legal, and financial consequences if ignored.
Fatigue cracking
Fatigue cracking, also known as alligator cracking, is one of the first visible signs of structural failure. It starts as thin interconnected cracks but quickly evolves into broken-up patches of asphalt. This usually happens because of poor base support, excessive loading from heavy vehicles, or moisture intrusion. Once these cracks appear, water starts seeping in, and the deterioration accelerates.
Depression and low spots
Depressions and low spots form in areas where the underlying subgrade wasn’t properly compacted during construction or where soil has settled unevenly. These areas trap water every time it rains, forming puddles that not only wear down the asphalt but also become hazardous for both drivers and pedestrians. Standing water also worsens during freeze-thaw cycles, causing additional cracking and surface damage.
Block cracking
Block cracking shows up as large rectangular segments across your pavement. Unlike fatigue cracking, which follows traffic patterns, block cracking typically spreads across unused or aged sections of asphalt. This usually happens when the pavement binder becomes dry and brittle due to age or temperature swings. If not sealed early, block cracking can lead to water infiltration and full sub-base erosion.
Ruts
Ruts develop in high-traffic areas where vehicles constantly drive along the same paths, like entryways, drive-thru lanes, and exits. Over time, the repetitive weight and movement create deep, narrow grooves in the pavement. These ruts affect vehicle suspension, create drainage problems, and are especially dangerous in winter when they fill with ice or slush.
Raveling
Raveling is another subtle but destructive issue. It happens when the asphalt binder starts breaking down due to oxidation, UV exposure, or poor initial mix. The surface begins to crumble, and loose gravel appears. This erosion reduces traction, looks unprofessional, and makes the entire structure vulnerable to further damage.
Potholes
Potholes are the most notorious and visible damage sign. They form when water enters through cracks and erodes the pavement from the inside. Combined with traffic pressure, the asphalt collapses into a hole. Potholes damage tires, cause trip-and-fall accidents, and frustrate customers. They’re also a major lawsuit magnet for commercial property owners.
Drainage failures
Drainage failures are one of the biggest underlying causes of many of the above issues. If water isn’t directed away from the surface correctly, either because of poor grading, blocked drains, or missing infrastructure, it will pool, seep, and break down your asphalt faster than anything else. Drainage issues often go unnoticed until the damage is widespread, and by then, the foundation may already be compromised.
Each of these problems doesn’t just affect how your parking lot looks. They directly impact safety, legal compliance, customer perception, and your repair budget. Now, let’s break down exactly how to fix these issues properly before they turn into money pits.
How to Fix These Parking Lot Problems (With Long-Term Value in Mind)
Fixing your parking lot isn’t about temporary patches; it’s about choosing the right repair method that adds structural strength, extends lifespan, and ensures you don’t keep paying for the same issue every year. Here’s how the most common problems are professionally addressed.
Fatigue Crack (Alligator Crack) Solution
Fatigue cracks signal that the surface and the base layer are compromised. A simple crack fill won’t solve this; it needs full-depth patching. The damaged area is saw-cut and removed, the base is re-compacted, and new asphalt is installed and leveled to blend with the existing lot.
This fix not only stops the spread of cracking but restores strength to the most stressed areas of your lot.
We perform full-depth asphalt repair with quality compaction and joint blending to prevent reflective cracking.
Depression and Water Pools Solution
Low spots are fixed by carefully removing the depressed asphalt, correcting the underlying base with new material, and adjusting the slope to improve drainage. Proper compaction is key to preventing the depression from returning.
Sometimes, regarding the lot or installing trench drains may be required if pooling is widespread. Our repair team uses laser-level tools to ensure water runoff flows efficiently; no more puddles.
Block Cracking Solution
These widespread cracks don’t always require full removal. Instead, they are cleaned, prepped, and sealed using rubberized hot-pour crack sealant that expands and contracts with the pavement.
In some cases, if the cracking covers more than 30% of a section, we may recommend resurfacing to restore the top layer uniformly. Our team has selected high-performance sealants that have withstood weather and traffic pressures for years.
Ruts and Wheel Track Damage Solution
To repair ruts, we mill out the grooved section and reinforce the subgrade with a stronger aggregate or asphalt binder mix. Then, new asphalt is compacted into place.
If the ruts run long or are paired with poor drainage, surface leveling and seal coating can be added to prevent recurrence. We upgraded the asphalt blend to handle heavier loads and prevent future indentations.
Raveling and Edge Deterioration Solution
Raveling is treated with a combination of seal coating and patching. If the surface is intact but eroding, seal coating replenishes lost binders and smooths out the surface. If raveling is too severe, surface milling and overlay are used.
This treatment protects your lot from further unraveling and extends its lifespan without full replacement. We use dense, commercial-grade coatings to protect high-traffic zones from oxidizing again.
Potholes Solution
We cut out the pothole area in a square or circular shape, repair the base, and compact fresh hot asphalt in layers. This ensures the patch bonds well and doesn’t come loose in a few months.
Pothole repairs should never be delayed; they are safety hazards and grow exponentially. Our hot mix and infrared bonding prevent edge cracking and blend seamlessly with your lot.
Drainage Problems Solution
If drainage failure is the root cause, we first inspect the slope and subgrade. From there, the fix may involve regrading, creating additional runoff channels, or installing trench drains or catch basins.
Proper drainage is what protects all other repairs from failing prematurely. We provide drainage correction services that align with local codes and maximize long-term durability.
These repair solutions don’t just “fix the problem”; they strengthen the overall system of your parking lot. Maintenance isn’t just about surface aesthetics; it’s about performance, compliance, and preserving your investment.
Why Parking Lot Maintenance Isn’t Optional; It’s Critical
Ignoring minor issues now always leads to bigger, more expensive problems later. Each factor below plays a huge role in damaging your asphalt, mentally, financially, and reputation-wise.
Harsh Weather: Freeze-Thaw Cycles Are Asphalt’s Worst Enemy
Heat causes expansion; cold causes contraction. These swings cause cracks that keep widening, especially in regions with extreme seasons.
Long-term effect: Surface breakdown, water infiltration, and full reconstruction costs ($20K+ for mid-size lots).
Water Damage: The Silent Destroyer of Pavement Integrity
Unsealed cracks allow water to reach the sub-base. Once there, it weakens the foundation, causing sinkholes and potholes.
Long-term effect: Accelerated decay and repair bills 4–5x higher than early maintenance.
UV Exposure: Asphalt Becomes Brittle Over Time
Sunlight dries out asphalt oils, leading to brittleness and surface erosion. Without a seal coat, you’ll need resurfacing far sooner.
Long-term effect: Full overlay needed within 5 years instead of 10+.
Vehicle Weight: Daily Wear Turns into Long-Term Damage
Trucks, delivery vans, and heavy SUVs apply thousands of pounds of pressure daily. This causes rutting and eventual base failure.
Long-term effect: Permanent grooves and drainage issues that require full repair.
Unprofessional Installation: A Flawed Foundation is a Time Bomb
If the original lot wasn’t compacted or graded correctly, all other maintenance becomes a short-term fix.
Long-term effect: Premature failure within 3–5 years, even with surface maintenance.
Neglecting Routine Maintenance: Waiting Always Costs More
Small cracks are cheap to fix. Potholes? Not so much. Waiting just one year can multiply repair costs by 3–6x.
Long-term effect: Liability claims, lost customers, and massive repair expenses.
How to Make the Smart Choice: Repair or Resurface?
Making the right financial decision means thinking long-term. Here’s how to figure out what makes sense for your parking lot and your budget.
Repair vs. Resurface: Which One is Good for You?
To avoid wasting money, ask these questions:
- What percentage of the lot is damaged?
Less than 25%? Repair.
More than 25%? Resurface. - Can the current base layer support future traffic?
If not, resurfacing or full reconstruction may be needed. - Is the damage surface-deep or structural?
Surface issues = crack sealing or seal coat. Structural = repair or resurface. - When was the last major maintenance?
If it’s been over 5 years, seal coating or full resurfacing may be overdue. - Do you want short-term savings or long-term peace of mind?
Repairs are cheaper now. Resurfacing gives you 8–10 years of strength.
Pro Tip: Always inspect the drainage and base strength before deciding. Small surface cracks can hide bigger foundation problems.
Frequently Asked Questions
How Long Does Asphalt Last With Proper Maintenance?
With professional care, like seal coating every 2–3 years and timely crack sealing, asphalt surfaces can last 20 to 30 years. However, neglecting even minor repairs shortens that lifespan by half. For high-traffic lots or harsh climates, annual inspections are recommended to stay ahead of early wear signs.
How Do I Know If My Parking Lot Is ADA Compliant?
You need clearly marked accessible spaces with correct dimensions, slope, signage, and direct access to pathways. Faded striping or worn signage can result in ADA violations, which carry fines of up to $75,000 for first-time offenses (Source: ADA National Network). Restriping is an easy and affordable fix to maintain compliance.
What If My Parking Lot Drains Slowly or Stays Wet After Rain?
Water pooling for over 24 hours after rain is a sign of poor drainage design or clogged stormwater systems. Ignoring this leads to sub-base damage, mold growth, and freeze-thaw cracks. A drainage inspection can identify slope problems or blocked outlets. We recommend installing trench drains, adjusting grades, or cleaning catch basins.
Is It Normal to See Cracks in New Asphalt?
Some minor surface cracks (called hairline cracks) can form within the first year due to temperature changes. However, widespread or deep cracking often points to poor installation, sub-base failure, or low-quality mix. These should be sealed immediately to prevent water damage.
Do You Repair Concrete Parking Lots, Too?
Our focus is strictly on asphalt surfaces, including maintenance, repairs, and protective treatments. For concrete parking structures, it’s best to consult a contractor who specializes in concrete patching, joint sealing, or slab replacement. Still unsure what material your lot is made of. Send us a photo, and we’ll help identify it before you spend a dime.
Common Misconceptions About Parking Lot Maintenance (Myths That Cost You)
“Sealcoating is Just Cosmetic”
Fact: Sealcoating isn’t about looks; it’s about preserving asphalt’s structural oils, protecting it from UV rays, oil spills, moisture, and oxidation. Skipping the seal coat cuts asphalt’s lifespan by up to 50%, making you spend more on early resurfacing.
“You Don’t Need Maintenance for the First 5 Years”
Fact: Asphalt begins aging the moment it’s installed. Surface protection and minor crack monitoring have been critical since year one. Even if no visible damage exists, UV exposure and temperature swings quietly degrade the binder.
“Cracks Can Wait Until They Get Bigger”
Fact: Small cracks are the #1 entry point for water, which destroys your base layer once it freezes and expands. Early crack sealing prevents 90% of long-term structural damage. Waiting turns a $200 job into a $5,000 repair.
“All Asphalt Is the Same”
Fact: Not all asphalt is created equal. Cheaper mixes degrade faster, especially under weight and weather pressure. Commercial-grade asphalt with proper compaction and binder ratios ensures durability. Always verify the material and techniques being used.
“DIY Repairs Are a Money Saver”
Fact: Cold patch kits or over-the-counter crack fillers don’t bond well to old surfaces, especially without proper cleaning or compaction. DIY fixes fail within a season, costing you more in repeat repairs. Professional equipment ensures sealants and asphalt bond deep and last longer.
“New Pavement Means No Worries”
Fact: Without immediate sealing, new asphalt oxidizes within 6–12 months, turning brittle and crack-prone. Many skip the first maintenance cycle, which is exactly when seal coating is most effective.
Fix Now or Pay More Later: Protect Your Lot, Reputation & Budget
Fatigue cracks, potholes, drainage issues, and raveling may look like surface problems, but they’re actually business risks, affecting safety, liability, customer trust, and your brand image. These issues don’t disappear; they worsen beneath the surface, becoming more expensive over time. The good news? With the right partner, you can fix them proactively and affordably, before they cost you even more.
If you’re aiming for long-lasting, professional results, Asphalt Coating Company has served Colorado since 1986, delivering code-compliant work that meets all DOT and ACC standards; no shortcuts, no risks.
Trusted by brands like COSTCO, King Soopers, TARGET, Lowe’s, The Home Depot, Travel Centers of America, and CRAMAX, we bring not just equipment but experience, precision, and a commitment to doing it right the first time.
We offer full-service parking lot maintenance, including Asphalt Repair, Crack Sealing, Striping, and Seal Coat Application. If your lot shows even one warning sign from this guide, now’s the time to act. Early maintenance saves money, prevents downtime, and keeps your property looking and performing at its best.
Book a Free Parking Lot Inspection Today and find out how to extend your lot’s lifespan while protecting your business’s reputation and bottom line.
Your parking lot won’t fix itself, but we will.